ダイカストとは?メリット・デメリットや材料ごとの違いを紹介
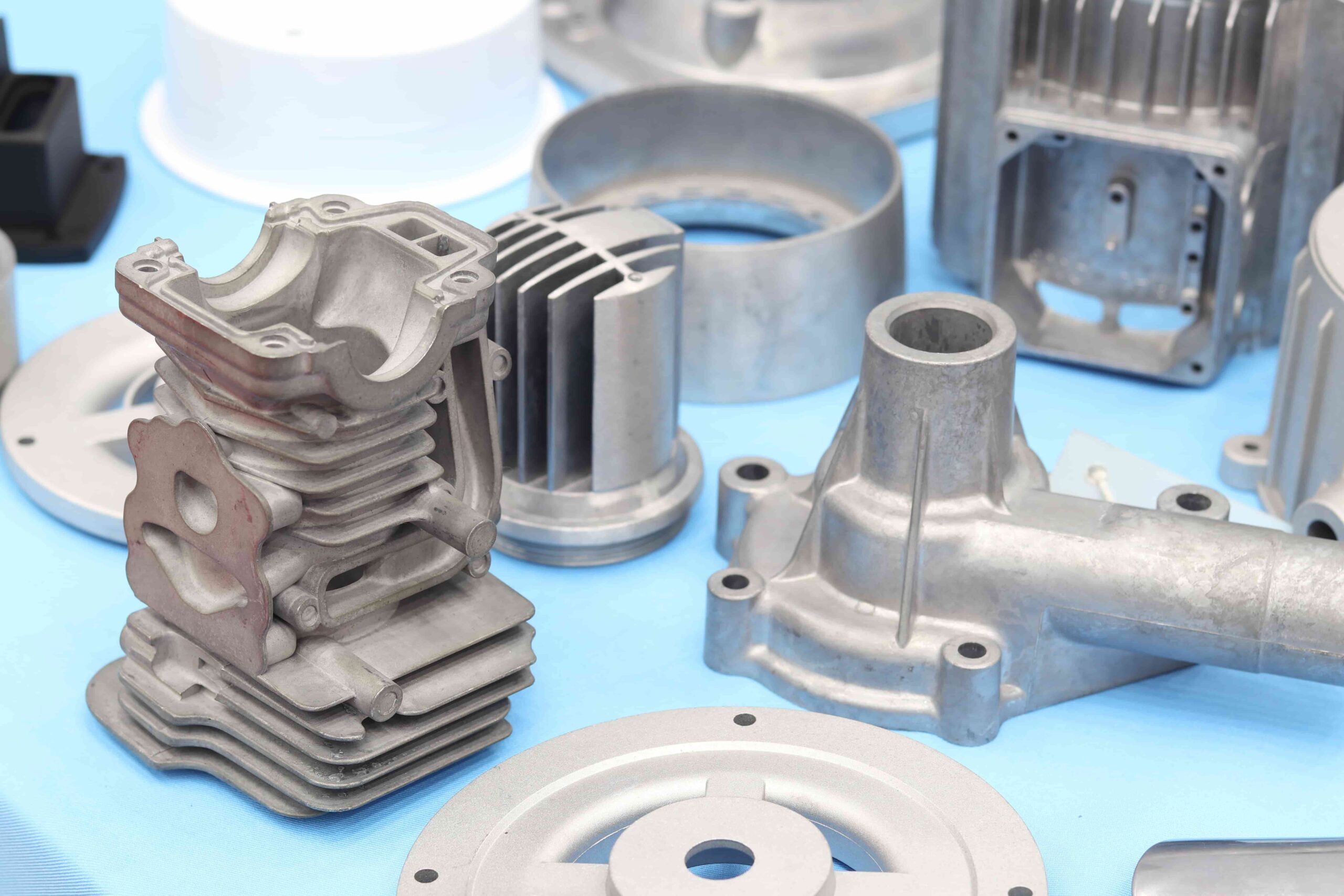
2024年8月6日更新
機電系エンジニア必見!!貴重なフリーランス案件はこちら ▶金属製品の製造において、ダイカストという単語はよく聞くと思いますが、どのような方法なのかご存じない方も多いのではないでしょうか。
そこで今回は、金属加工の一つであるダイカストについて、原理や他の金属加工と比べたときのメリット・デメリット、材料ごとの特性の違いなどについて解説します。
ダイカストとは
ダイカストは、アルミを始めとするさまざまな金属を溶かし、金型に入れて成形する特殊な鋳造品のことです。
ダイカストの特徴は、強度の高い金型に、溶解した金属を高圧で充填する所にあります。高速かつ高精度な金属成形が行えることから、アルミや亜鉛などの合金を作る際に幅広く用いられています。
ダイカストを使うメリット
ダイカストにはメリットが多く、様々な金属加工で使われます。そのメリットについて詳しく解説します。
大量生産が可能
一番のメリットは、金型を使うため、安価かつ高速に大量生産が可能ということです。複雑な形状であっても切削加工のように煩雑な作業が必要なく、一工程で製品が作れます。ダイカストは一度の成形にかかる時間が数十秒程度と短く、同時に複数の製品を作ることも可能なので、量産性は非常に高いです。
また、ダイカスト用の金型は非常に強度が高く、数万回以上連続して使用できるため、他の鋳造法と比較しても大量生産向きと言えるでしょう。
寸法精度が高い
ダイカストのメリットとしては、その寸法精度の高さも見逃せません。通常、鋳造品は切削加工よりも精度が低く、表面に凹凸やバリが発生するため、寸法精度を高めるためには追加工が必要となります。
しかしダイカストは材料を高圧で充填することから、寸法精度が非常に良く、表面の仕上がりも美しいです。切削にこそ及ばないものの、通常の用途であれば追加工が不要な精度が保てるので、量産工数やコストの削減にもつながります。
ダイカストのデメリット
ダイカストはメリットの多い加工法ですが、もちろん完璧な成形方法ではありません。ここからはダイカストの主なデメリットについて説明します。
切削には強度で劣る
ダイカストは溶かした金属を充填して成形しますが、材料と共に空気やガスが入るため、製品内部に鋳巣と呼ばれる空洞が生じます。鋳巣があると強度が下がるため、切削と同様の強度は維持できません。また、鋳巣が膨張して欠陥の原因となることから、ダイカストでは熱処理が行えず、強度を上げる対策も難しいです。
ただ、鋳巣の発生は鋳造圧力や湯口のサイズ、充填速度など、製造条件を最適化することによって減らせます。真空ダイカストや無孔性ダイカストなど、鋳巣を減らす特殊ダイカスト法の開発も進んでおり、強度が高く熱処理が可能なダイカストの生産も行われ始めています。
金型にかかる費用が高い
金型の制作費が高く、初期費用が高額になるのもデメリットです。ダイカストの金型製作は難しく、製作にはさまざまなノウハウが必要となります。オーダーメイド品で製品ごとに製造条件を最適化する必要もあり、工数も多くかかります。
他にも、高圧の鋳湯充填や、大量生産に耐える耐久性も求められることから、金型製作には数百万円単位での費用がかかるのが現状です。量産コストは安価なので、数万個単位での大量生産を行う場合はいいですが、少量生産を考えている場合は別の手法を選んだほうが良いでしょう。
ダイカストの種類と特徴
現在、ダイカストに使われる金属はアルミニウム、亜鉛、マグネシウムの3種類にほぼ限られています。それぞれの特徴と、用途について解説します。
アルミダイカスト
まず、最も一般的で、ほとんどのダイカストに採用されているのがアルミニウム合金です。アルミニウムは、重量が鉄の1/3という軽さが特徴で、さらに緻密な酸化被膜を作るため、耐食性や強度に優れています。
加工性のよさや毒性がないことによる加工の容易さ、経年による変形も少ないなど、非常にバランスがいい特性を持つため幅広い用途で使われています。特に軽量さから、自動車や航空機の部品として大量に利用されているほか、熱伝導性の高さ、非磁性などから電子機器の筐体としても人気が高いです。
亜鉛ダイカスト
亜鉛ダイカストは、寸法精度が最も高く、追加工なしで複雑な形状の製品を作れるのが特徴です。また、アルミダイカストと比べると強度は劣りますが、薄肉での成形にも向いています。鋳肌のなめらかさにも優れており、めっきや表面処理によって美しい質感の製品が簡単に作れるため、装飾用の部品製造に有用です。
また、亜鉛は、他の金属とくらべて融点が低く、製造時の温度を下げられることから、金型寿命が非常に長くなるというメリットもあります。アルミダイカストの金型より数倍寿命が長くなることから、金型製造のコストを下げたい場合におすすめです。
マグネシウムダイカスト
最近、その比重の軽さから注目を浴びているのがマグネシウムのダイカストです。アルミニウムの2/3と、鋳造に使える金属の中でも最も軽いのが特徴で、軽量化への要望が強い携帯電話やパソコンなど、精密機器の筐体に用いられています。
強度はアルミニウムや亜鉛に劣り、耐食性も低いというデメリットがありますが、加工性の良さ、振動吸収性の良さなどのメリットも持っているため、軽さと丈夫さを求める機械部品への採用が進んでいます。
ダイカストの作り方
最後に、ダイカストの製造方法について解説します。工程は合金の溶解、金型での成形、冷却・取り出し、検査・追加工の4つの工程に分かれます。
合金の溶解
ダイカスト製造の最初の工程は、材料となる合金の溶解です。材料にはインゴッドや、スクラップ材、バリなどのリターン材を用います。溶解によって得られた鋳湯の品質はダイカストの品質に直結するので、厳密な品質管理が行われています。
まず重要となるのは温度管理です。温度が低いと材料の溶解に時間がかかりますが、高すぎると酸化物の割合が上がっていくため、適度な温度を保ち効率的に材料を溶解しなければなりません。
同様に、材料の成分調整も重要です。溶解後に成分をチェックし、必要に応じてシリコンや銅などを添加します。また、大気中の不純物が混じると品質の低下に直結するので、脱ガス処理、脱酸処理などの処理も必要です。
ちなみに、溶解炉に材料を入れる際は、水蒸気爆発を防ぐために、溶解炉の余熱や乾燥をしっかりと行う必要があります。
金型に溶湯を圧入し成形
鋳湯の準備が整ったら、金型に流し込み鋳造を行います。成形の品質を上げるため、材料の充填前にエアブローなどによる金型の清掃と、潤滑剤、離型剤の塗布を行っておきましょう。
その後金属の充填を行っていきますが、ダイカスト法の場合、先に金型を閉めてから、プランジャーを用いて高速に鋳湯を打ち込むことで、金型内部を高圧に保ちます。製造条件にもよりますが、ホットチャンバーダイカストマシンの場合は数MPa、コールドチャンバーダイカストマシンの場合は数十MPa程度の圧力を持つことが多いです。
一気に材料を充填することで、複雑な形状であっても金型内部に材料がいきわたり、さらに金属が冷えるタイミングも均一に保てるため、品質の高い鋳造品ができあがります。
また、充填の際には金型の温度管理も重要です。温度が低すぎると湯じわなど欠陥が生じる原因となり、高すぎると金型にダメージが蓄積するため、最適な温度を把握しておく必要があります。
冷却、取り出し
鋳湯を金型に充填したら、冷えて金属が固まるまで放置します。この時間のことをキュアリングタイムと呼びます。キュアリングは短すぎると型崩れの原因となり、長すぎると熱収縮によって金型から外しにくくなるので、適切な時間を決めておきましょう。
冷却が終わったら、押し出しピンで製品を金型から外し、ロボットなどを使って金型から取り出します。金型の清掃からダイカスト取り出しまでの時間をサイクルタイムと呼びます。
品質チェック、後処理
金型からダイカストを取り出したら、品質チェックを行います。ダイカストは製造条件によって品質は大きく変わるため、内部組織構造や強度、各種欠陥の有無などを確認し、十分な品質を持っているか判断します。
品質に問題がないことを確かめたら、後処理を行って完成です。後処理工程では、ダイカストの形状や表面構造をより正確に、美しく整えるため、下記のような作業が行われます。
トリミング
材料投入部分や押出ピン部など、ダイカスト金型の構造上、製品の形状以外で出来てしまう余計な部分を取り除く工程です。トリミングプレスやハンマーなどで対処します。
バリ取り
離型時に生じた微細な割れや、金型のずれによって生じるバリを取り除く工程です。ショットブラストや研磨、科学的な処理、工具を使った手作業などで対処します。
ひずみ取り
金型から取り出した時などに生じる、ダイカストの歪みやねじれなどを取り除く工程です。詳細な計測を行いながら、ハンマーやプレス機などを用いて修正します。
表面処理
熱処理やめっき、塗装、化成処理など、さまざまな表面処理を行う工程です。強度や耐久性、装飾性を大きく高められるため、仕上げ加工として行われます。
まとめ
今回は、特殊な鋳造法であるダイカストについて、特徴や材質ごとの違い、製造工程などについてお伝えしました。
ダイカストは寸法精度が非常に高く、金型があれば高速に製造できることから、大量生産する機械や筐体などに幅広く用いられています。
金型が非常に高価で、大量生産するまでの条件出しが大変ですが、その分のメリットは十分あるため、生産量や他の製造方法とのコスト差を比較し、ダイカストで製造するのが最適か検討しましょう。
フリーランス×機電系エンジニア!高単価求人はこちら ▶
機電系求人はこちら
-
設計技術者(樹脂、金属部品)
-
- 単価
-
40~50万円
-
- 職種
- 機械設計
-
詳細を見る
-
-
FPGAの設計開発:電気電子設計
-
- 単価
-
70~80万円
-
- 職種
- 電気電子設計
- スキル
- ・FPGA論理設計、RTLコーディング、論理検証環境構築、論理検証・RTLコード:VHDL・論理検証ツール:Siemens製Questa/ModelSIM
- 地域
- 東京
- ポイント
- #高単価
-
詳細を見る
-
-
UI画面の設計業務:電気電子設計
-
- 単価
-
64〜万円
-
- 職種
- 開発
- 電気電子設計
- スキル
- 必要スキル: ・電源回路は複数回経験し、設計動作確認など、一人でもある程度やるべきことが分かる。 ・数十頁のデータシートを読み、要求仕様(タイミング/電圧など)が理解できる ・その他左記の回路の種類の中で、回路設計の実務経験が1回以上ある。 ・回路修正ができる(半田付け、ジャンパー処理)
- 地域
- 関西
- ポイント
- #業務委託#駅近
-
詳細を見る
-
-
【急募】工作機械メーカーにおける自社製品の制御設計
-
- 単価
-
40~50万円
-
- 職種
- 電気電子設計
- スキル
- 基本的なPCスキル産業用機械・装置の電気設計経験
- 地域
- 山梨県
- ポイント
- #業務委託
-
詳細を見る
-