表面実装(SMT)における製造工程の流れを分かりやすく紹介!
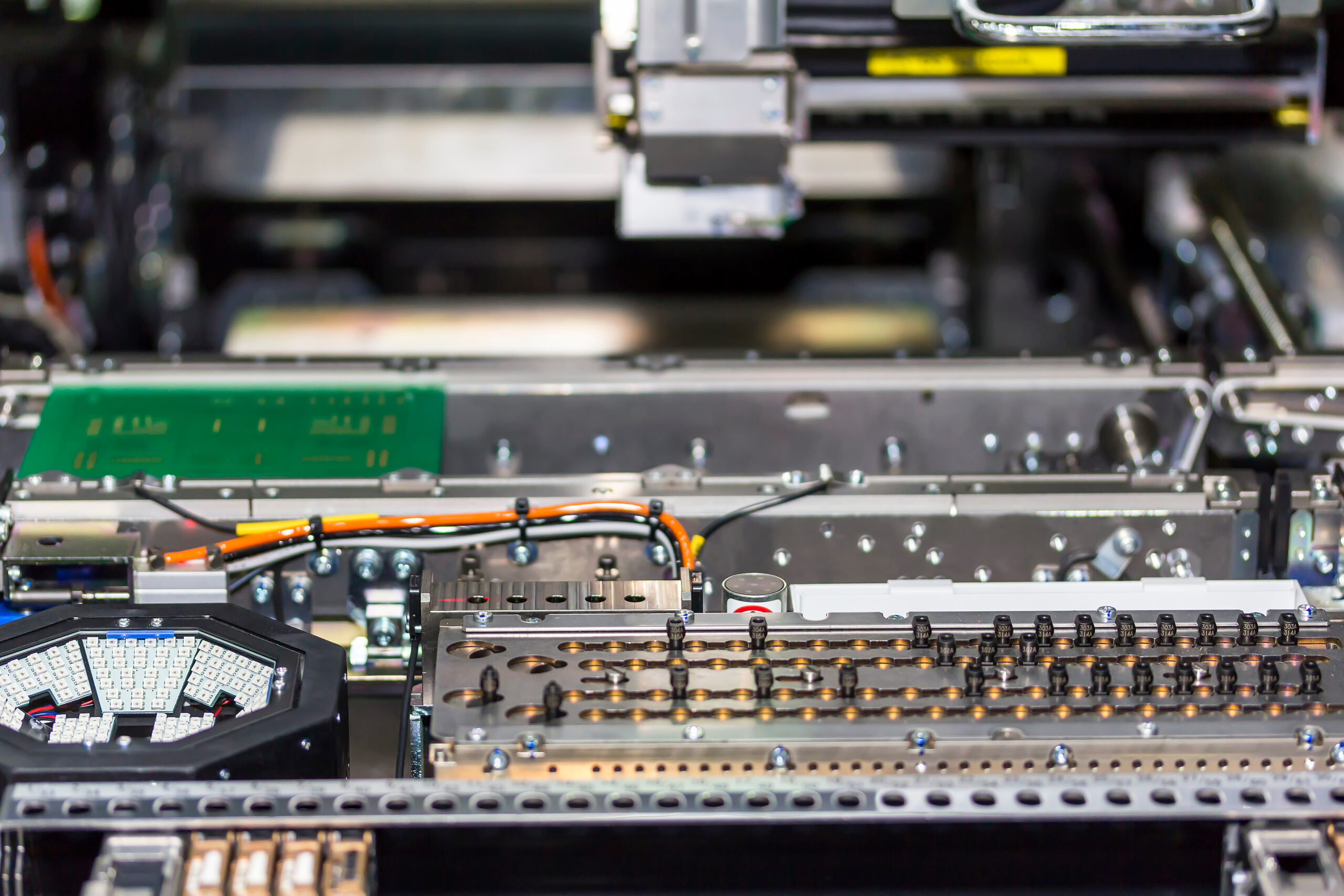
2023年10月10日更新
機電系エンジニア必見!!貴重なフリーランス案件はこちら ▶電子回路の製造工程において、「表面実装」は電子部品をプリント基板に取り付ける重要な工程です。本記事では、表面実装の製造工程がどのようになっているか、詳しく解説します。
表面実装とは
表面実装とは、プリント基板に部品を取り付ける代表的な方法です。かつて電子部品は、端子としてリードと呼ばれる足を伸ばし、プリント基板に挿し込むことで導通させていました。しかし、基板に穴を開けなければならないため、部品や基板サイズを小さくできないといった問題がありました。
この問題を解決するために開発されたのが、部品にリードを付けず、プリント基板の表面にある銅箔パッドと部品を直接はんだ付けする手法です。基板に穴を開けず、基板表面に部品を載せてはんだ付けできることから「表面実装」と呼ばれるようになったのです。
今では、表面実装を自動化する設備が整っており、超高速・高精度な実装が行えるようになったため、ほとんどの電子回路で表面実装が採用されています。
表面実装の流れ
それでは、表面実装をどのように行っているか、流れを一つずつ説明しましょう。
プリント基板(PWB)を用意する
まずは、部品を実装するためのプリント基板を用意します。プリント基板は、部品同士を設計通りに接続するため、基板表面や内部に銅箔パターンを配線した部品のことです。プリント基板上には、部品を基板上に正しく実装できるよう、はんだ付けを行うための「ランド」と呼ばれるパターンがあります。ランド形状は部品実装時のはんだ品質や歩留まりを向上させるため、技術的な工夫がなされています。
プリント基板自体の製造工程が知りたい方は「プリント基板(PCB)とは?基礎知識から製造工程まで解説!」にて解説しているのでご覧ください。
基板クリーニング
プリント基板を用意したら、部品実装を開始する前に、基板についたホコリやゴミなどを取り除くためのクリーニングを行います。部品実装装置にコンパクトなクリーニング装置が付随しており、風で吹き飛ばしてゴミを取るのが一般的です。細かい作業ではあるものの、不良率に大きな差が出るため、ゴミが付着しにくい工程を組むなどの工夫も重要となります。
クリームはんだ塗布
クリーニングが終わったら、実装工程を開始します。まず初めに行うのは、電子部品を基板に貼り付けるためのはんだを塗布する工程です。表面実装では、ペースト状で常温でもクリームのような柔らかさを保つ「クリームはんだ」を用います。そのままクリームはんだを塗布すると余計な場所にもはんだが付着するため、CADデータを元に作った「メタルマスク」という治具を使い、ランドのみにはんだが付くように工夫します。
クリームはんだは温度や湿度など、外部環境によって塗布される状況が変わるため、品質を保つのが最も難しい工程です。メタルマスクも、端子間の短絡やはんだのクラックやボイド、はんだボールの発生などを避けながら、正確にクリームはんだを塗布するためのノウハウが詰まっています。
部品実装
クリームはんだを塗布したら、プリント基板上に電子部品を載せていきます。「チップマウンター」と呼ばれる、自動で電子部品を所定の場所に載せる機械を使うのが一般的です。実装する電子部品はリールで購入し、「フィーダー」と呼ばれる機械にセットすることで、チップマウンターに供給します。あとは基板の種類ごとに専用のプログラムを組めば、自動でチップマウンターが部品を認識し、所定の場所に取り付けてくれるのです。
部品の搭載位置はカメラの画像認識技術で把握し、ノズルヘッドで小さな部品を吸着し着実に運ぶことで、高速・高精度な部品実装を実現します。ちなみに、チップマウンターは実装を自動でしてくれるため量産は簡単ですが、部品点数が多いと段取りが複雑になります。試作など、生産数が少ない基板を作る場合や、電子部品にバラ品を使う場合はチップマウンターが対応できないため、手で実装部品を載せる必要が生じます。
リフローはんだ付け
部品を載せ終わったら、熱をかけてはんだを溶かすためリフロー炉にプリント基板を入れます。はんだの溶融温度は、はんだは183℃、鉛フリーはんだは217℃となっているため、リフロー炉は内部を250℃程度に加熱することで、はんだをしっかりと溶かします。
ただし、一部の電子部品は、はんだが溶ける高温環境下に置いておくと壊れてしまうので、高温状態が一定時間以下になるような温度調節が欠かせません。一般的には、150℃程度に加熱するプレヒートを行い、さらに250℃への加熱を30秒程度以内に抑えることで、熱によるダメージを最小限に抑えています。
他にも、はんだを正しく溶かし、クラックやボイドなどが発生しないよう、温度上昇速度や加熱時間が厳密に定められているのがほとんどです。ちなみに、リフロー炉という名称は、溶かしたはんだを直接流してはんだ付けを行う「フロー炉」の対となることから名付けられています。
表面実装後の工程
以上が表面実装の工程となりますが、プリント基板を完成させるまでには「リード部品実装」「外観・導通検査」といった工程が入ります。
リード部品実装
コイルや電解コンデンサなど、一部の部品はサイズが大きく、リード部品しか製造されていません。リード部品は表面実装ではんだ付けできないので、表面実装後の工程で実装を行っていきます。まず、リード部品を基板に挿入し、余分な長さのリードを切り取ります。この工程は手実装で行われることが多いです。基板への挿入が終わったら、フロー炉にてはんだを塗布します。
フロー炉は、基板の裏面に溶けたはんだを直接接触させてはんだ付けを行う方式です。フラックスを塗布した後に基板をヒーターで温め、リード部品の近辺に溶けたはんだを流すといった工程で実装を行います。
外観・導通検査
部品実装が全て終わったら、基板が正常に動くか検査します。実装後の検査では、部品の実装やはんだの形状に不良がないか確かめる「外観検査」と、回路に電流が正常に流れるかを確認する「導通検査」を行うのが一般的です。
外観検査は、画像認識による自動検査が普及しています。ただ、認識の精度には限界があるため、人による目視検査も同時に行っていることが多いです。最近では、AIの学習機能を使い、自動検査の品質を上げる取り組みも行われているため、将来的には完全な自動化が期待されています。
導通検査は、基板のテストパッドに電極を当て、各パターンのキャパシタンスや抵抗値をチェックして正しく導通しているか確かめる検査です。検査項目は数多くあるため、量産時には実装基板に合わせた設計を行い、自動で導通検査を行う自動検査機を使います。
まとめ
今回は、電子回路の表面実装工程について詳しくお伝えしました。表面実装は、リードのない部品をプリント基板上に載せ、はんだで固定する実装方法です。現在ではほとんどの基板製造において表面実装が選択されているため、表面実装用の装置や技術は確立しています。ただし、はんだ付けの品質や歩留まりを上げるためのノウハウがそこかしこに詰まっているので、条件を変更する際は細心の注意が必要となることを覚えておきましょう。
フリーランス×機電系エンジニア!高単価求人はこちら ▶
機電系求人はこちら
-
設計技術者(樹脂、金属部品)
-
- 単価
-
40~50万円
-
- 職種
- 機械設計
-
詳細を見る
-
-
FPGAの設計開発:電気電子設計
-
- 単価
-
70~80万円
-
- 職種
- 電気電子設計
- スキル
- ・FPGA論理設計、RTLコーディング、論理検証環境構築、論理検証・RTLコード:VHDL・論理検証ツール:Siemens製Questa/ModelSIM
- 地域
- 東京
- ポイント
- #高単価
-
詳細を見る
-
-
UI画面の設計業務:電気電子設計
-
- 単価
-
64〜万円
-
- 職種
- 開発
- 電気電子設計
- スキル
- 必要スキル: ・電源回路は複数回経験し、設計動作確認など、一人でもある程度やるべきことが分かる。 ・数十頁のデータシートを読み、要求仕様(タイミング/電圧など)が理解できる ・その他左記の回路の種類の中で、回路設計の実務経験が1回以上ある。 ・回路修正ができる(半田付け、ジャンパー処理)
- 地域
- 関西
- ポイント
- #業務委託#駅近
-
詳細を見る
-
-
【急募】工作機械メーカーにおける自社製品の制御設計
-
- 単価
-
40~50万円
-
- 職種
- 電気電子設計
- スキル
- 基本的なPCスキル産業用機械・装置の電気設計経験
- 地域
- 山梨県
- ポイント
- #業務委託
-
詳細を見る
-